Diego Paredes
Create Your First Project
Start adding your projects to your portfolio. Click on "Manage Projects" to get started
EGS20G - Gravity TEC Racing
Collegiate Engineering Team Vehicle
Photography
Role
Chassis and aerodynamics Engineer > Chief Engineer
Date
February 2021 - June 2022
Location
Monterrey, Nuevo Leon
The EGS20G was a motorless racing car for the TEC Racing – Gravity team, designed for the “Gravity Race Car” Series in Mexico. The series consists of two 5km races in different cities throughout Mexico with an average altitude change of 400m accelerating the cars to speeds up to 100 km/h.
I joined the Gravity – TEC Racing team and by extension the EGS20G project as a chassis and aerodynamics engineer where I got a solid understanding of tubular chassis design, SolidWorks weldments, beam static stress analysis, aerodynamic principles, and aero package design through theory, design, and analysis. Despite my heavy involvement within my team, I quickly found myself reaching out to other subsystems within the team, driven by curiosity and awe in the complex system that is a race car.
Because of the Covid-19 pandemic, during this period manufacturing was suspended and our in-person activities were limited, this would later lead to integration and manufacturability issues due to the lack of hands-on experience with the needed manufacturing methods.
I was chosen as the next chief engineer for my design sense and involvement in most of the team’s subsystems. Having just returned from the COVID-19 pandemic, we needed to build a competitive vehicle from scratch with an undertrained team. Through effective communication, analysis, redesign, and collaboration I was able to lead the team to build the EGS20G in under 2 months.
Throughout the two-month timeframe, we did not have enough time or trained personnel to manufacture the vehicle without the direct involvement of the leadership team. This meant that I got hands-on experience in manufacturing all vehicle subsystems, gaining valuable hands-on engineering experience. This experience, detailed below would become invaluable for future vehicle design and is at the core of what I consider to be one of my strengths as a young engineer: Mechanical design FOR manufacturing.
For the spaceframe chassis, I mainly worked with low-carbon steel, cutting and notching the tube using our school's conventional milling machine. These tubular sections along with plasma-cut steel tabs were welded together with a mix of stick and MIG welding, depending on availability. The suspension arms, pushrods, and steering column were manufactured in a similar way, with the addition of bushings, couplers, and other components produced and modified in the lathe.
The fiberglass bodywork was produced through an open mold layup, however, due to the tight schedule the plugs could not be finished in time to the needed surface finish, and a plastic wrap was needed to protect the plugs during layup, reducing the part quality greatly.
Finally, the braking and traction subsystem was by far the most problematic, due to cost limitations the vehicle had to be adapted to fit a very different braking system than was originally planned. Among the redesigns needed the steering knuckles, wheel hubs, half shafts, and even the brake disks had to modify, a daring task in the small university lathes.
Although we were able to produce a full vehicle, an accomplishment I will always be proud of, the compromises we had to make due to time and monetary constraints led to a frankly uncompetitive vehicle.
Having learned from our past mistakes, we analyzed the original EGS20G concept, which by now looked very dissimilar from the vehicle we produced, and identified key issues and strengths. We decided our time would be better spent producing a new vehicle from scratch, taking into account manufacturing-oriented design and creating a truly competitive vehicle based on fundamental engineering principles. And thus, the EGS23G was born



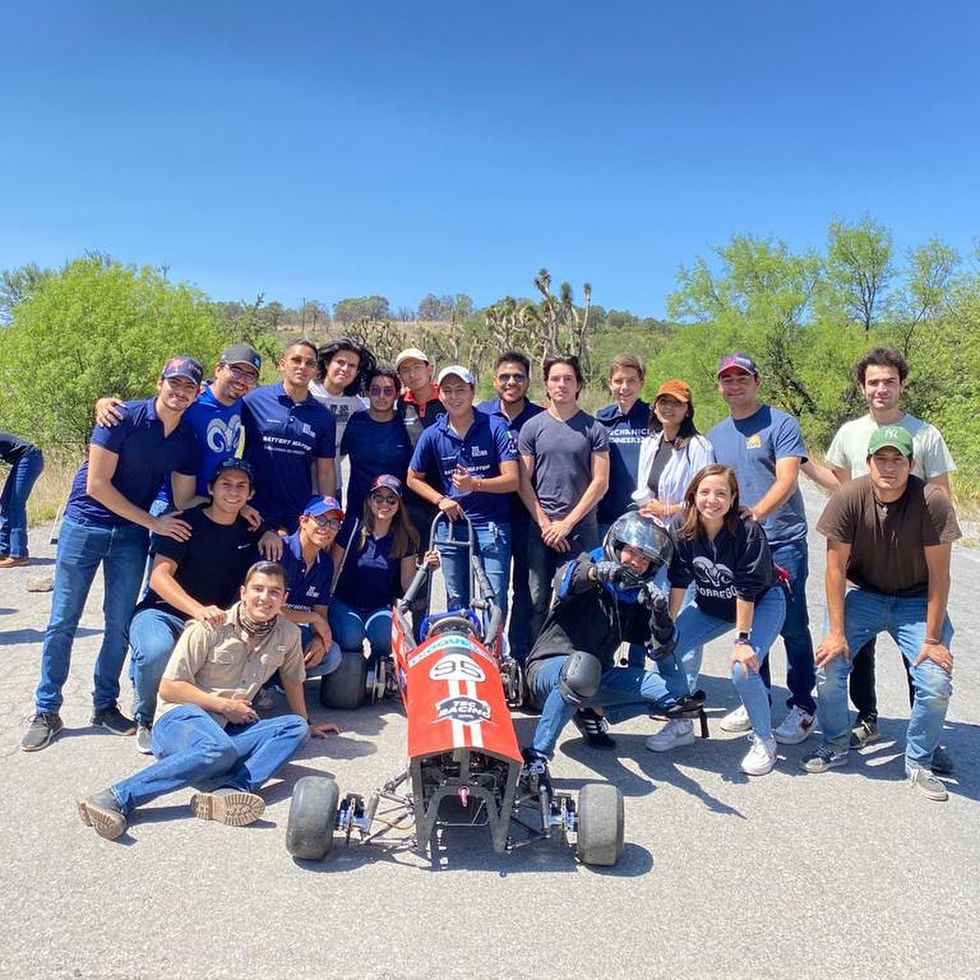

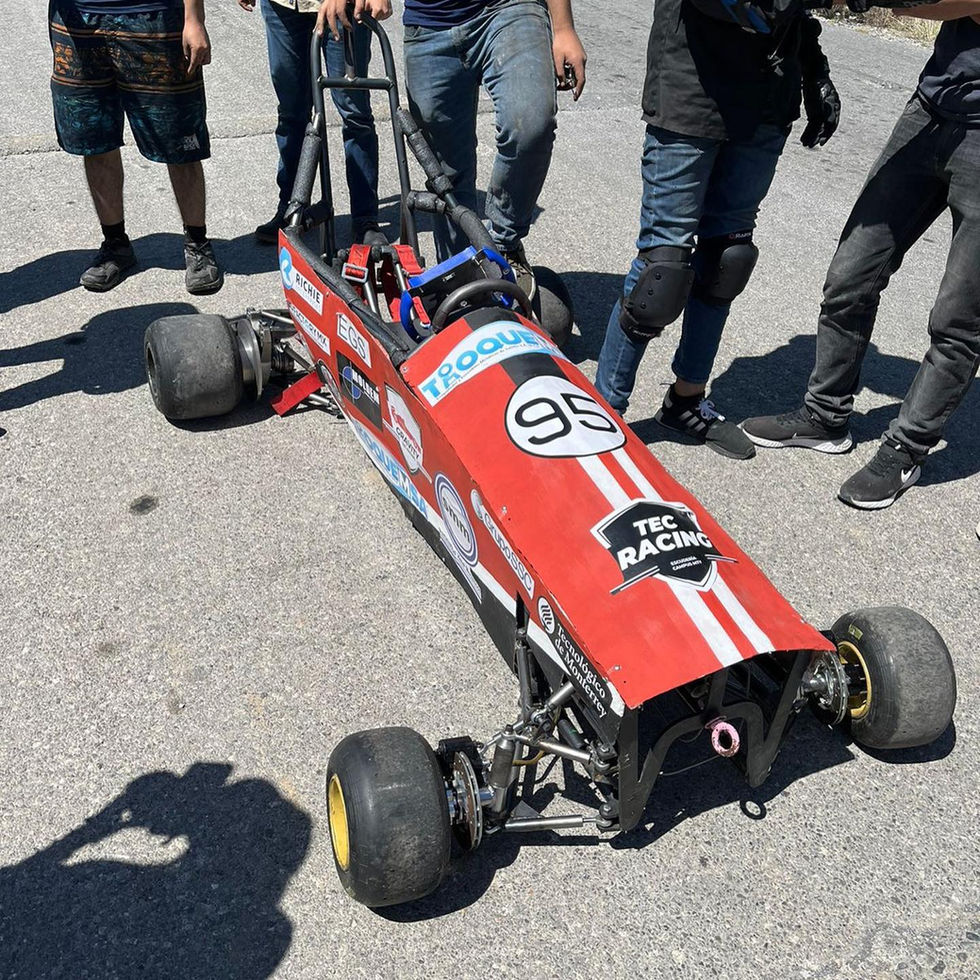















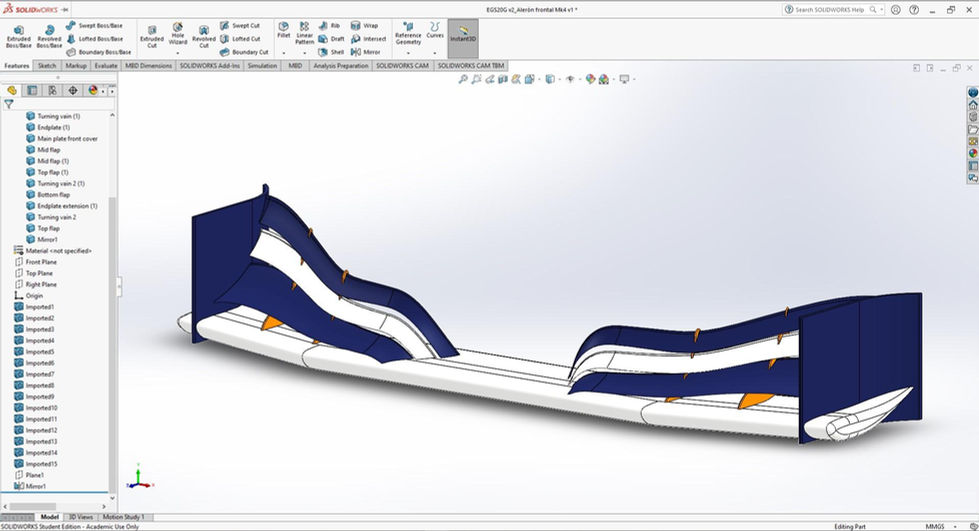

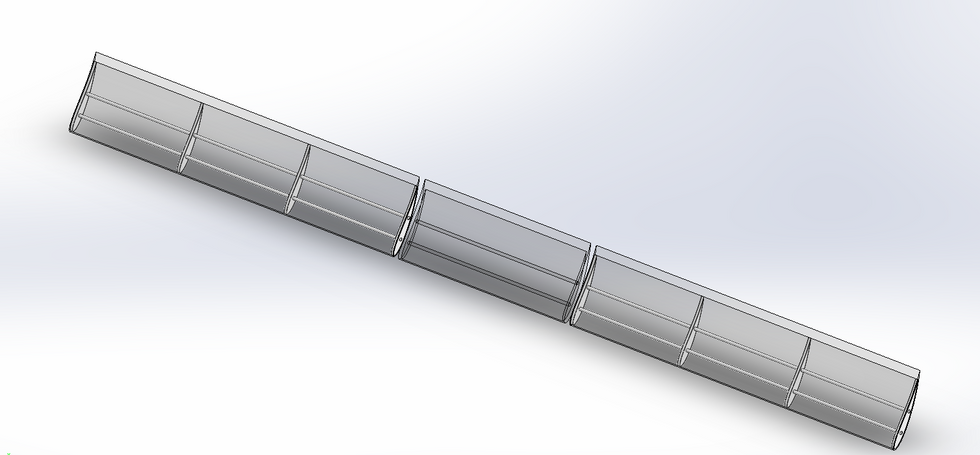







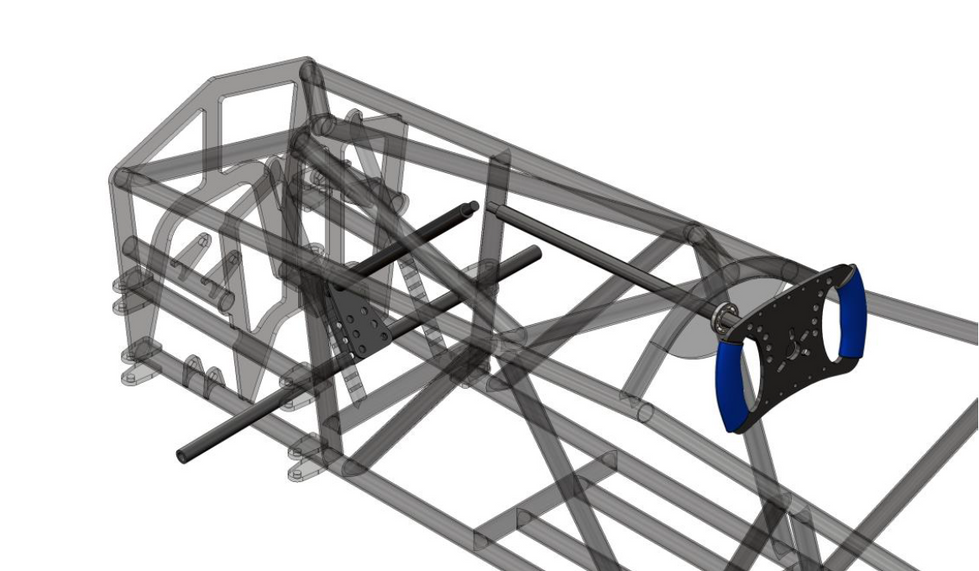

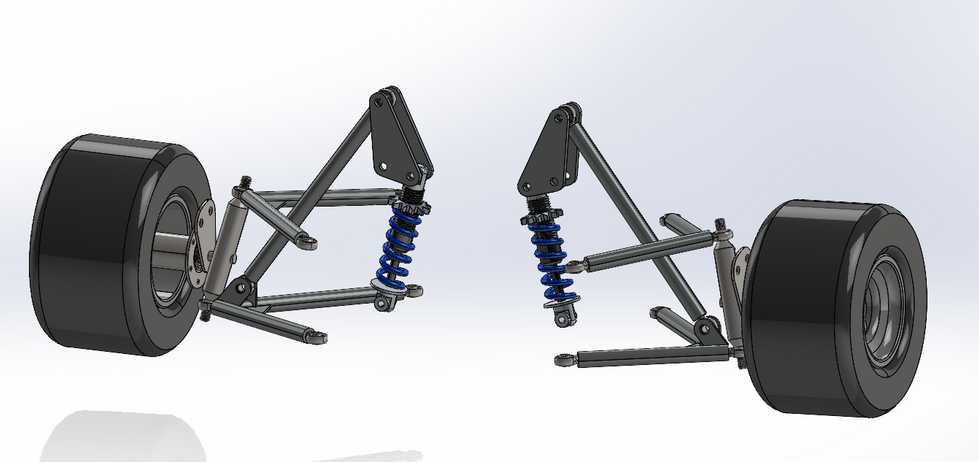